Den viktigaste skillnaden mellan PFMEA och DFMEA är att PFMEA hjälper till att analysera potentiella fel i en viss process i en affärsenhet medan DFMEA hjälper till att analysera potentiella fel i en design av en produkt.
Metoden för FMEA (Failure Mode Effects Analysis) hjälper till att identifiera potentiella fellägen för en process vid driftledning och en design på produktutvecklingsstadiet i ett system och kategorisera fel baserat på sannolikheten och svårighetsgraden av felet. Felläge hänvisar till eventuella defekter eller fel i en design, process eller en artikel som påverkar kunden. "Effektanalys" syftar på studiet av konsekvenserna av misslyckanden.
Vad är PFMEA?
PFMEA står för Process Failure Mode Effects Analysis. Denna metod kan identifiera potentiella fellägen i processer på operationsnivå. I allmänhet genomför ett tekniskt erfaret team PFMEA. Den grundläggande processen är att samla in adekvata data för orsakerna till fellägen för att rätta till eller minimera effekterna av felläget.
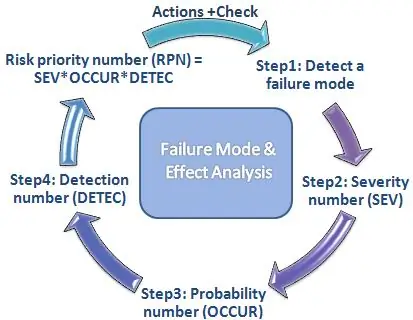
Dessutom är PFMEA ett strukturerat verktyg som används av alla typer av organisationer. Det hjälper till att bygga upp effekterna av fellägen och prioriterar de åtgärder som krävs för att lindra risken. PFMEA dokumenteras och presenteras innan några nya processer lanseras för att minska potentiella faror. Dessutom är det också möjligt att tillämpa detta på rådande processer för att uppnå ständiga förbättringar av systemet.
Vad är DFMEA?
DFMEA står för Design Failure Mode Effects Analysis. Denna metod hjälper till att identifiera potentiella fel i produktdesigner i utvecklingsstadiet. I de flesta fall använder ingenjörer detta som en procedur för att undersöka möjligheten av designfel i en verklig situation eller användning.
De primära verktygsingenjörerna för DFMEA är en DFMEA-matris. Denna matris presenterar en struktur för sammanställning och dokumentrelaterad information inklusive tekniska specifikationer, utfärdandedatum, revisionsdatum och teammedlemmar. Generellt sett är DFMEA ett lagarbete av teknisk expertis och förmodligen ett tvärfunktionellt team. Dessutom förlitar sig DFMEA inte på processkontroller för att övervinna möjliga designfel
Vilka är likheterna mellan PFMEA och DFMEA?
- PFMEA och DFMEA är två typer av analys av fellägeseffekter.
- Grundläggande steg i DFMEA och PFMEA liknar varandra, men de har två olika tillämpningar.
- Både DFMEA och PFMEA indikerar möjliga fel, riskernas allvar, befintliga kontroller, rekommendationer och förbättringar efter rekommenderade åtgärder.
- Det yttersta målet för båda är att minska eller undvika stora brister i produkter och produktion.
- De här metoderna kan också sänka kostnaderna för design eller drift.
- Dessutom kanske vissa misslyckanden inte kan åtgärdas hos DFMEA. Dessa fel kan överföras till PFMEA för att vidta nödvändiga kontroller för produktförbättring.
Vad är skillnaden mellan PFMEA och DFMEA?
Den största skillnaden mellan PFMEA och DFMEA är att PFMEA involverar processer medan DFMEA involverar produktdesign. Det primära syftet med DFMEA är att upptäcka potentiella fel i produktdesign medan det primära målet för PFMEA är att avslöja potentiella fel i processer. Den grundläggande granskningen av DFMEA genomförs med hjälp av produktschema, medan PFMEA genomförs med hjälp av ett processflödesschema. En annan skillnad mellan PFMEA och DFMEA är att PFMEA sker på operativ nivå medan DFMEA sker på utvecklingsstadiet.
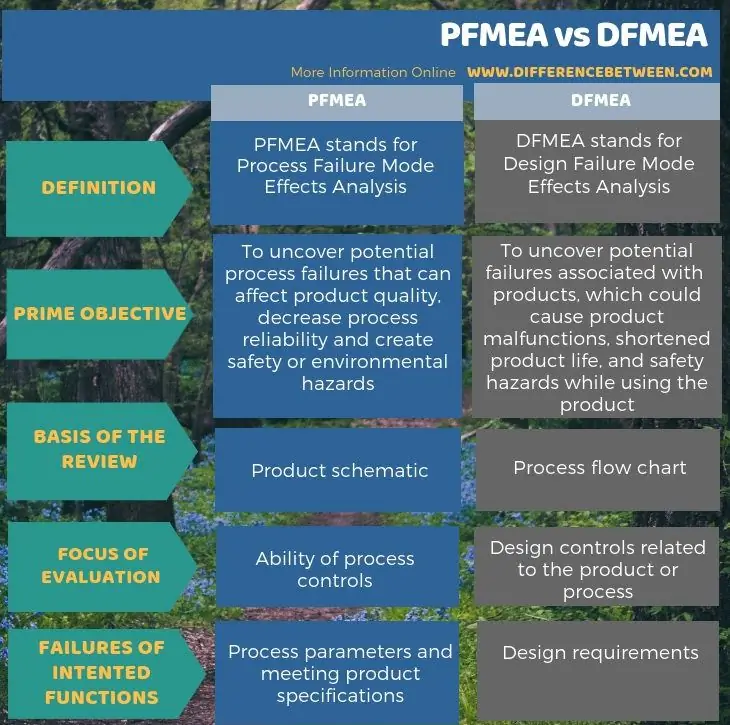
Sammanfattning- PFMEA vs DFMEA
Den viktigaste skillnaden mellan PFMEA och DFMEA är att PFMEA hjälper till att analysera potentiella fel i en viss process på driftsnivå medan DFMEA hjälper till att analysera potentiella fel i en produktdesign på design- och utvecklingsnivå. Dessutom kommer dessa metoder att sänka produktionskostnaderna och även eventuella misslyckanden vid produktlanseringar.